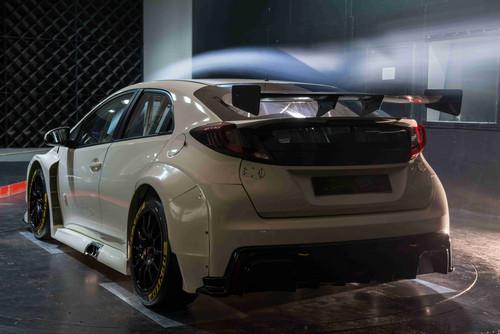
The HORIBA Full Scale 6 Component External Wind Tunnel Balance is a platform-type balance. A computer program is used to calculate the forces Fx (Longitudinal-Force), Fy (Lateral-Force), Fz (Vertical-Force) and the three moments Mx (Roll-Moment), My (Pitch-Moment), Mz (Yaw-Moment) from the six force sensor signals. This ‘computer-separation’ method is to be distinguished from other balance types using mechanical separation methods.
Robust and maintenance free balance construction
The advantage of the HORIBA balance system is a very robust, simple, long term stable and maintenance free construction of the balance. No lever systems and no hydraulics are used. Also, no tare compensation system is necessary.
Highest accuracy of 0.02 % to 0.05 %
Even small force components in the order of 1 N (100 gram) can be measured while a static preload of approx. 150000 N (15 tons) in Vertical-Force direction is applied caused by the mass of the balance platform, wheel spinner masses and vehicle mass. By using high quality load cells and a precise high resolution digital amplifier system highest measurement accuracies in the order of 0.02 % to 0.05 % of full measuring range can be achieved. The measuring range of vertical force is up to 15000 N. Additionally, the cross interference of different force components is eliminated by special calibration and data evaluation methods.