EV 2.0 belongs to EV actual family to introduce modularity. EV 2.0 is ideal for monitoring in-situ the health of plasma, process stability, leaks, arcing and abnormal plasma behavior as well as detecting the endpoint in OES or INT configuration.
General features
- Multi-Configurations to fit your needs
EV 2.0 is available with: - Three different software packages
- Several choices of spectrometer, from low to high resolutions
- Several configurations to manage Optical Emission Spectroscopy and/or Multi-wavelengths Interferometry diagnosis.
- Several configurations to manage Single chamber or cluster tool (up to 6 chambers)
- To discuss which best suits your application, please contact us.
- Sensor Management
Using HORIBA excellence in optics and spectroscopy proprietary managers allow to interface several sensors from OES to interferometry, with openness for external integrations.
- Sigma_P for real-Time Monitoring and Endpoint
Sigma_P© software allows rapidly configuring recipe and then creating robust endpoint detection: - Using Windows 10 based Software platform, intuitive user interaction permits to deal with spectra or directly with wavelengths along time. The Software contains an opened library with classical plasma emission wavelengths.
- A simple Recipe Editor allows the user to build efficient recipes, including Multiple wavelengths algorithms, signal arithmetic and filtering, plus Endpoint/Health Monitoring condition(s) and decision(s), using a Formula Editor, with help online integrated.
- Up to 8 curves can be displayed on the same screen to monitor specific species evolution, Endpoint & chamber health monitoring at the same time.
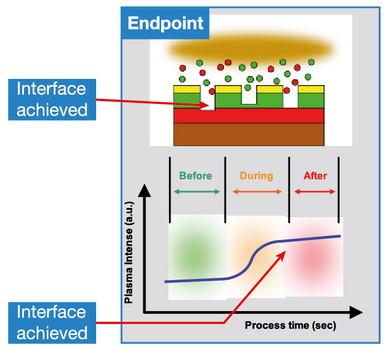
- Recipe Management
Unified concept permits to setup recipes in a fluent and user-friendly Excel-like Recipe Editor.
With Sigma_P software expansion settings feature, many compatible algorithms for special signal detection and detection of signals with poor S/N ratios are included and can always be expanded.
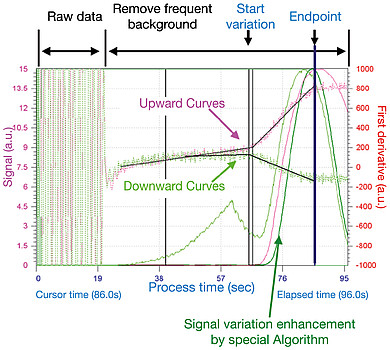
- SQL Management
Chamber Database, Tool Databases are embedded close to the sensor and accessible online, by operator, by recipes, by statisticians, by HM and APC servers, by distant process engineer office.
- Reprocessing Manager to playback raw data
To allow instant replay of mathematical treatment for instrumentation optimization but also scripted automatic reprocessing of multiple data runs for process validation, HM / APC extensions, parametric studies.
This data can also be sent directly to HORIBA for analysis and optimization.
- Active Recipe Manager
Extensions allow data exchange Run to Run, Wafer to Wafer, Lot to Lot, Chamber to Chamber for enhanced production control.
- Statistical Process Control in situ
Statistic engine allowing recipes to self-compute production metrics, default values, triggered by direct user but also from host or engineer desk.
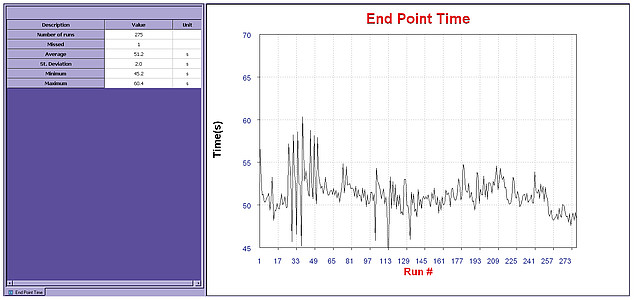
- Automation Data Link Manager
Design flexibility to interface chambers, equipment mainframes, fab hosts, fab servers using middlewares: Remote Control (RS 232, TCP/IP, PIO), SECS, HSMS, Fab LAN, Fab e-mailing, and other protocols.
- Advanced Algorithm Manager
Combination of powerful external math tools to the native recipe math formula editor and in situ math calculator.
- Distributed and Configuration
Thanks to long history in instrumentation clusterisation, this new concept allows to configure instruments from standalone engineering to integrated chamber controller up to full cluster tools.
- Health Monitoring & APC
Design openness to integrate rules based and in recipe integration of user scenarios depending on their HM / APC vision, technics and tools.
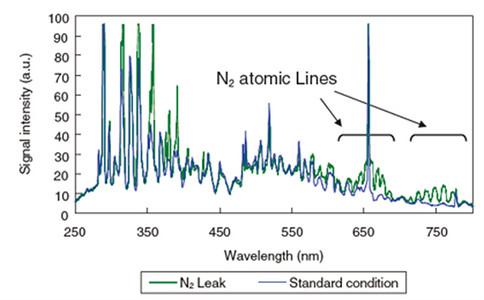
- Recipe Designer 2.0 for OES
To ease OES Engineering Flow, AI Machine Learning not supervised method to ease OES engineering and create Strong Endpoint recipes.
In real time, algorithm deals with selected wavelengths previously chosen and then calculates (by minimization fit) a temporal rupture position and a rupture intensity. The rupture point represents the statistical best fit where residual variance is optimum. When rupture intensity is greater than a predefined threshold, Endpoint is reached.
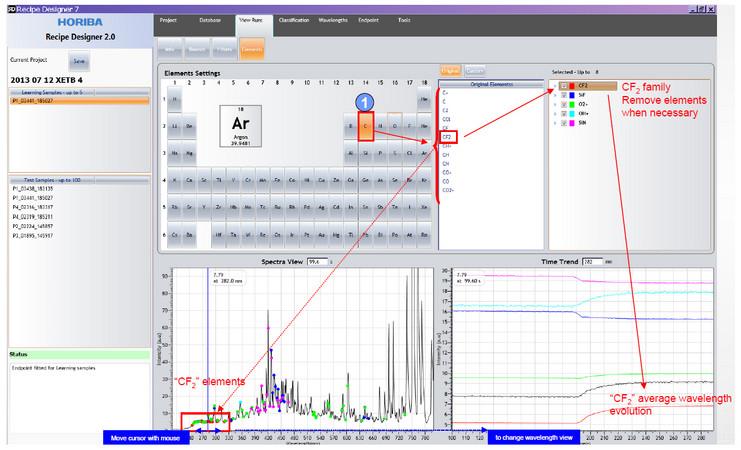
Process Engineer has simply 4 parameters to manage: Time window, Wavelengths range, Rupture direction (Upward if species appear or Downward if species disappear) and Threshold.
Then, Recipe Designer© permits to extract automatically relevant wavelengths containing on raw spectra, characteristic of plasma change like interface achieved, impurities detection, Endpoint found, …
And then an Endpoint recipe is automatically built and transferred to Sigma_P in one click. We cannot approach complicated endpoint without this easy–to-use, but powerful, tool!
- Kinetic Modeler for Interferometric engineering.
Theoretical Interferometric curve according to piling structure (each layer is characterized by its material, thickness, and Etch/deposition rate) and Wavelength used. It permits to obtain reference curve before real engineering on wafers
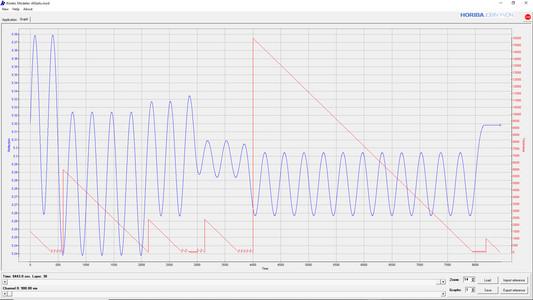
EV 2.0 PC Applications
Generality
Regarding CCD based OES (Optical Emission Spectroscopy) or Interferometry (Laser or Multiwavelength using broad Flash Lamp source), endpoint detection mostly consists in three steps:
- selection of the relevant wavelengths that carry the information about the transition (interface detection) or thickness/depth/remaining thickness
- a real-time data filtering (in the broad sense) and the construction of an endpoint indicator,
- a series of tests to confront the algorithm to the reality of production fluctuations.
To address these new requirements, HORIBA has developed a unique generation of Sensor (Hardware and Software), based on OES and/or interferometry, for Endpoint, fault detection, Chamber health monitoring and Advanced Process Control (APC) adaptable to all etchers, to help engineers and Fab’s to manage actual and future products and technologies.
Optical Emission Spectroscopy: OES
EV 2.0 to take full advantage of the OES wealth
EV 2.0, using Optical Emission Spectroscopy (OES), allows the study of spectra emitted by atoms and ions with optical transition in the UV-VIS-NIR regions. OES, as a rich qualitative tool, is the only mean for process engineers, without any intrusive plasma perturbation:
- To gather additional relevant plasma parameters like particle density (reactive species, by-products), electron density, electronic and ionic temperature,
- To understand Plasma Chemistry, physical phenomenon’s and control plasma interaction with sample, wall chamber, … during plasma DRY etching, sputtering, PECVD, cleaning, Failure analysis, …
- To operate chamber qualification
- To troubleshoot process problems, like impurities, leaks, contamination, process drifts
With EV 2.0, Horiba offers a versatile solution from R&D to industrial applications for:
- General Monitoring for plasma dry etching and deposition: Data collection, analysis, comparison using internal emission library, process identification, uniformity control
- Cleaning processes
- Chamber Health Monitoring: Chamber qualification, conditioning, matching and troubleshooting, Chamber gas purity control and leak detection, post Preventive Maintenance checks, failure analysis…
- Advanced Endpoint Process Control: Fully Automated Endpoint/Run to run control/Fault Detection Classification/health monitoring system to improve yield and increase productivity in semiconductor manufacturing.
- Endpoint
- Wafer R2R Control
- Detection of interface
- Process Uniformity
- Low Open area
- Minimize overetch and protect wafer against underetch
- Production reproducibility
- Quality: Yield & Throughput
- Chamber Health
- Chamber/Process stability control during Wet Clean cycles
- Plasma Spectral Monitoring
- Reference (Library) for Chamber fingerprinting, piping, quantitative comparison
- Process drift, Trend analysis
- Detection of oversized signal
- Preventive Maintenance
- Reduce Tool Downtime
- HORIBA is providing WIN10 PRO, 64bits PC with HORIBA Software dedicated to OES monitoring and endpoint
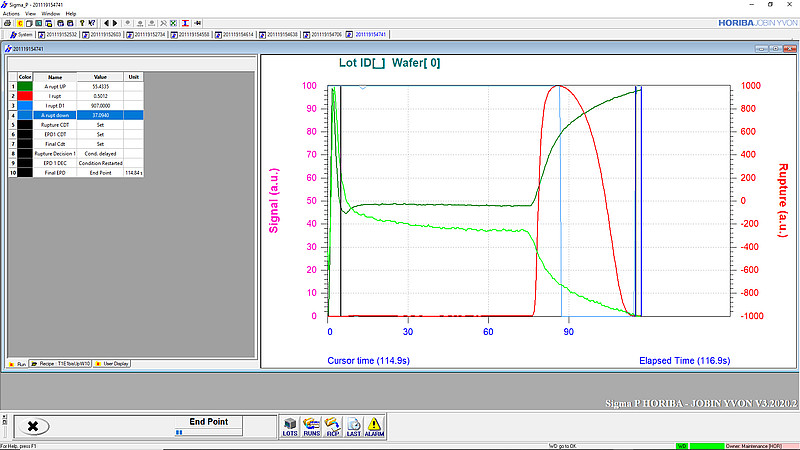
- Key Add-on: Recipe Designer 2.0 to ease Endpoint and process Engineering
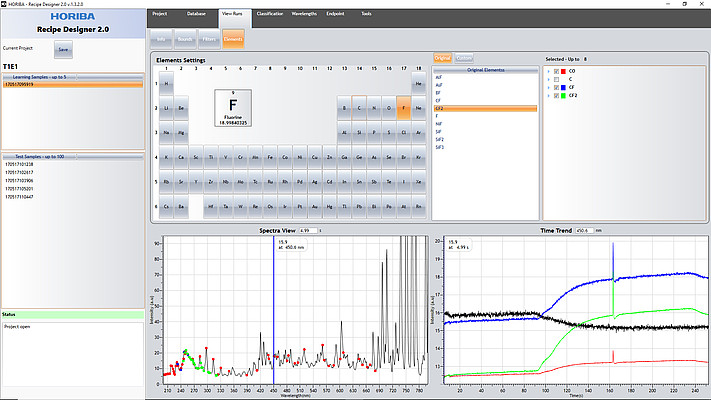
Interferometry: INT
EV 2.0 INT for Real-Time accurate and reliable Thickness/depth information
Besides plasma, Sample information is also complex. EV 2.0 INT (as LEM-CT), mounted on any process chamber with direct top view of the wafer,allows to obtain local information on optically semi-transparent, multi-layers structure. This allows the etch rate and thus etched thickness to be monitored in real time, providing enhanced process control for a wide variety of processes. Additionally, interfaces can be detected by their change in reflectivity.
Based on the interferometry technique, EV 2.0 INT is ideally suited to etch/deposition rate monitoring and endpoint detection, providing high precision detection of Fringes counting, film thickness, trench depth, interfaces…
- Interference occurs when monochromatic light hits the sample surface, resulting in different optical path lengths due to film thickness and height variations in the film.
- HORIBA is providing WIN10 PRO, 64bits PC with HORIBA Software dedicated to interferometric monitoring and endpoint
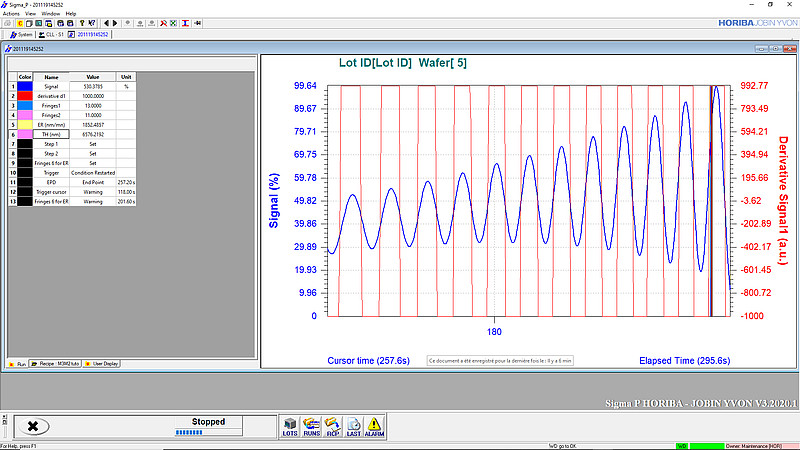