Hayabusa2 Project
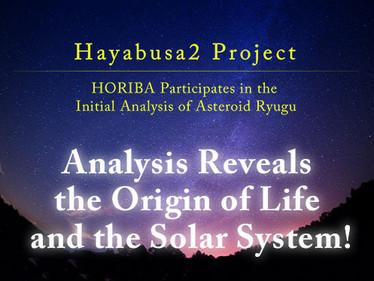
Les sociétés du groupe international HORIBA proposent une large gamme d'instruments et de systèmes pour des applications telles que la R&D automobile, les processus et la surveillance de l'environnement, le diagnostic médical in vitro, la fabrication de semi-conducteurs et la métrologie, ainsi que diverses mesures scientifiques pour la R&D et le contrôle qualité. La marque HORIBA est reconnue pour la qualité et la fiabilité de ses produits.